References
With the UNTHA XR3000C, Saubermacher Dienstleistungs AG has found the optimal shredding solution for the single-phase shredding of commercial and bulky waste. High throughputs, high resistance to non-shreddables, easy and safe maintenance, a high level of plant availability and reduced energy costs were the decisive factors behind the decision of this recycling company.
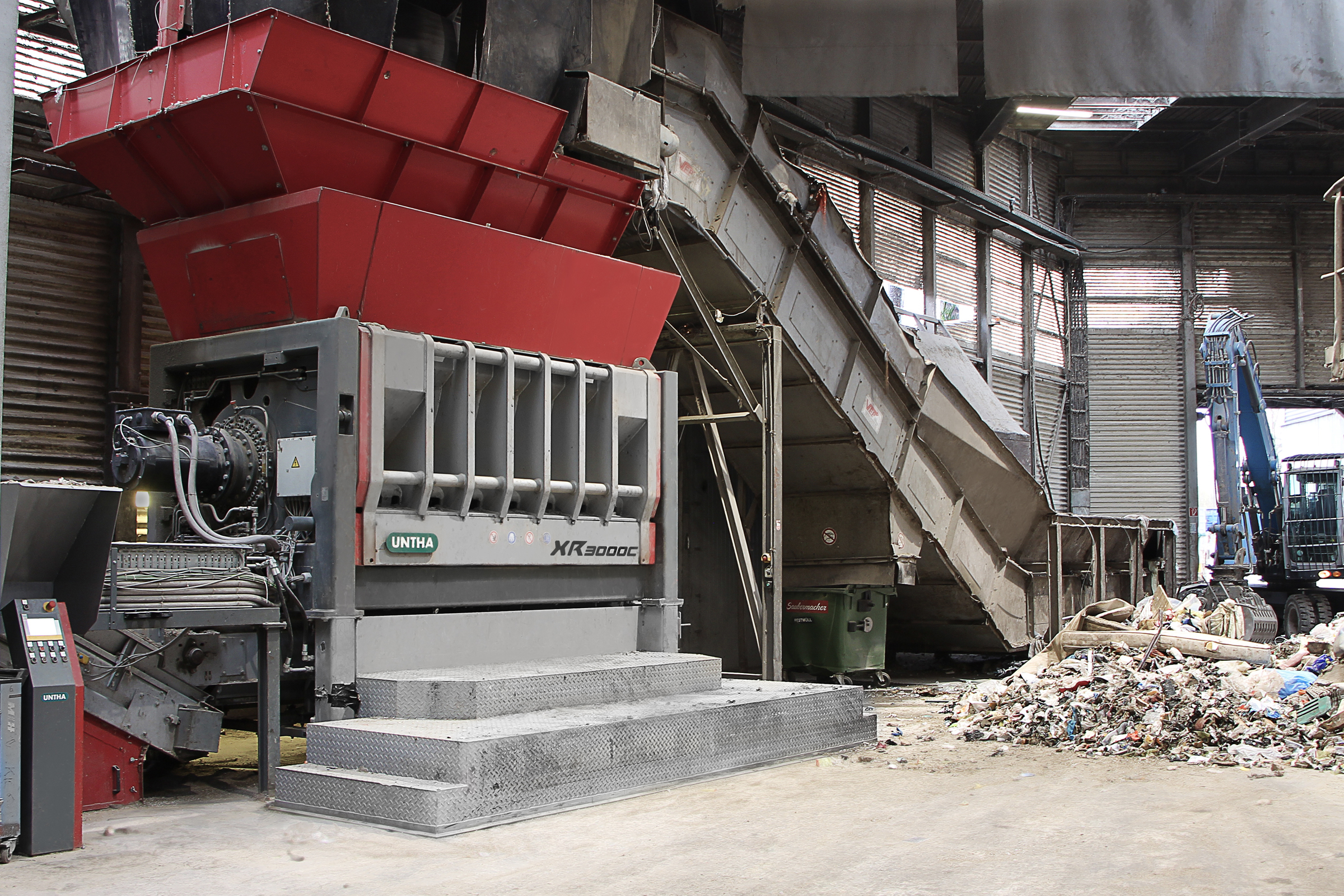
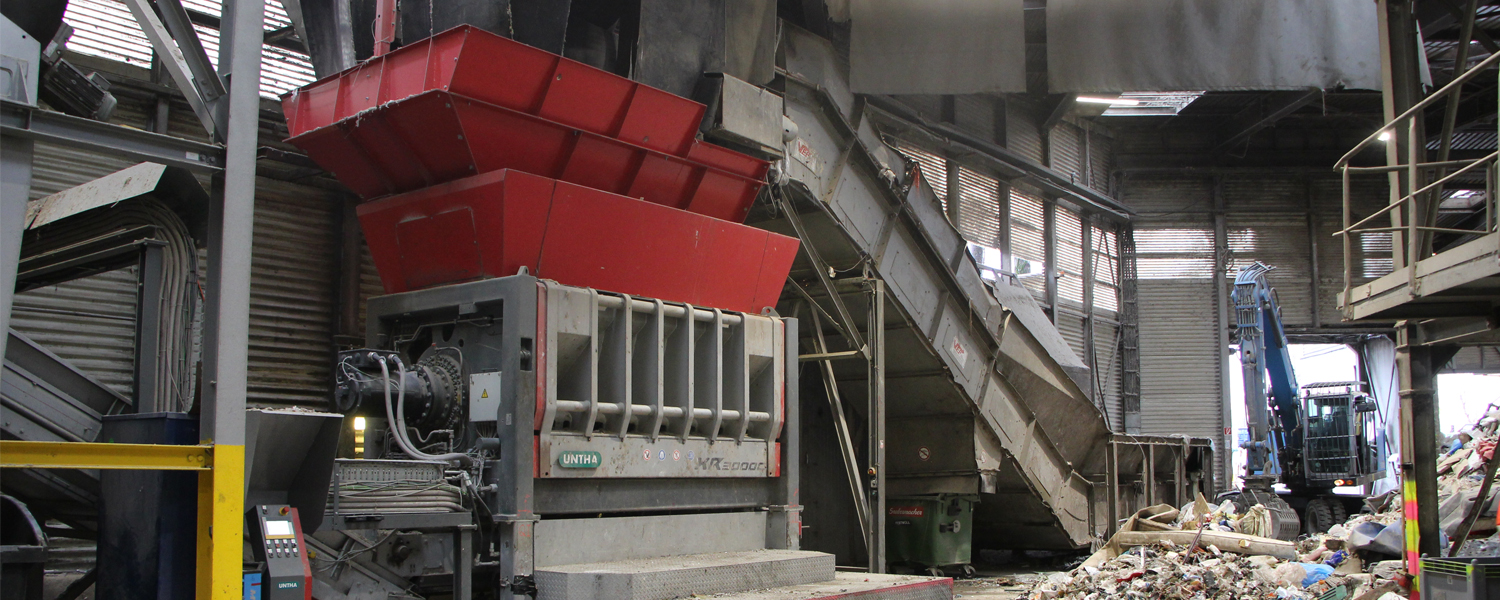
Saubermacher Dienstleistungs AG specialises in the disposal and processing of recyclable materials. The company operates in more than 7 countries and employs 3350 people. At the splitting facility in Vienna, 90,000 tonnes commercial and bulky waste are processed into alternative fuels for the cement industry every year.
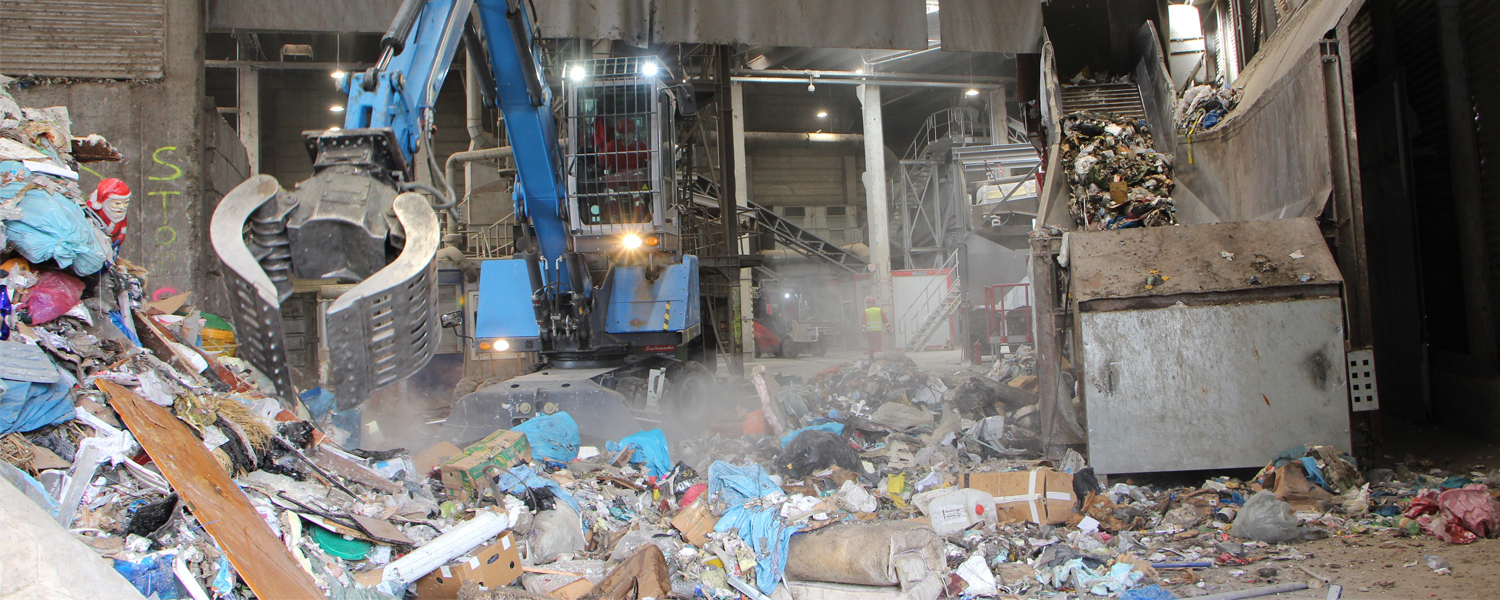
In line with new market requirements, the company was looking for a robust, energy-efficient single-phase shredding solution to turn commercial and bulky waste into a fraction of less than 80mm, at a throughput rate of at least 20 tonnes/hour. The plant is operated in three
shifts, requiring a high level of reliability for the shredder as well as high resistance towards foreign matter, which appears in the material processed on an almost hourly basis.
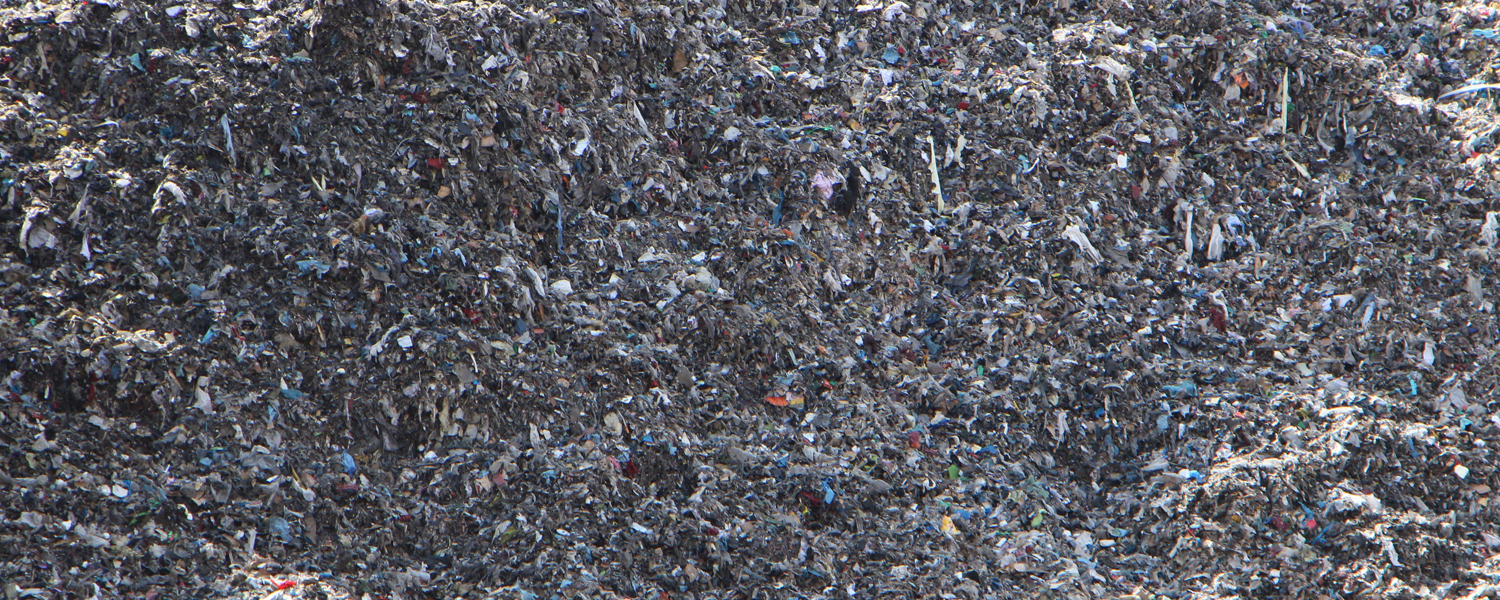
After a successful test run, the company decided in favour of single-phase shredding of commercial and bulky waste using the XR3000C. Non-shreddable objects, a frequent occurrence in these material flows, are removed speedily and safely via the dedicated exit door. As the rotor runs at slow speed, it stops immediately when a non-shreddable object is encountered, protecting the cutting system from serious damage. As the cutting chamber is easily accessible, the shredder is fully operational again in no time, ensuring a high level of plant availability.
The strength of the UNTHA Eco Power Drive is reflected in low energy costs in particular, which become particularly noticeable in 3-shift operation. The hard surfacing of the rotor significantly increases its availability, in particular with abrasive materials.
After several trial runs using machines by different manufacturers, we opted for the XR3000C as it impressed us the most. One important aspect was the energy-efficient drive concept, which we really liked and which has more than proven its worth in the meantime.
Wolfgang Kremsl
Head of Investment and Technology International
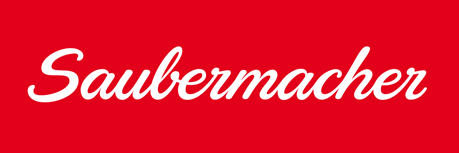
After the company had tested several shredders, they finally opted for the XR3000 C. Non-shreddable objects are easily removed via the dedicated exit door, reducing downtime for the entire plant. An additional safety coupling protects the cutting system and the power train from damage caused by non-shreddables.
The highly efficient UNTHA Eco Power Drive lowers energy costs, in particular in multi-shift operation, and has significantly reduced energy consumption compared to the previous unit.
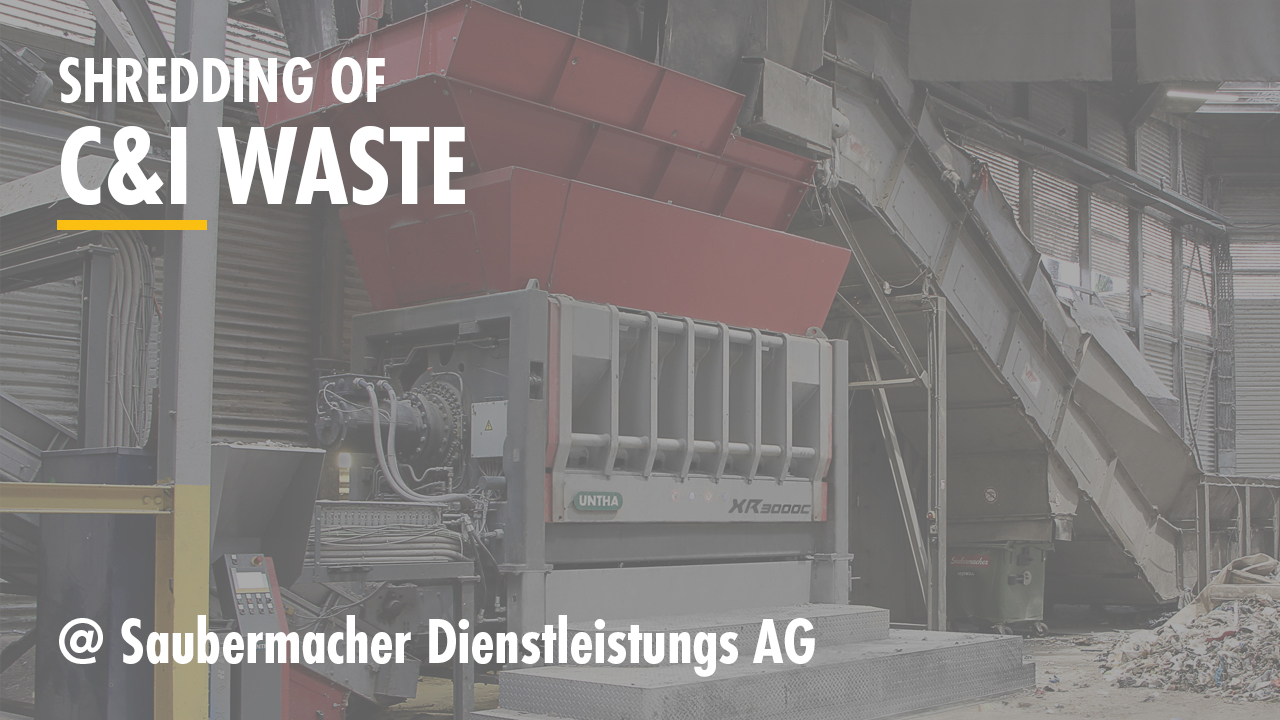