Cost-efficient tire shredder
Are you looking for the best tire shredder on the market? The XR tire shredder is an energy-efficient machine that processes scrap tires, car tires, and truck tires into small pieces for further processing. An overband magnet can separate up to 80% of the wire, which creates a high-value end product for use in cement plants as Tire-Derived Fuel (TDF) or other markets.
The XR can be used to produce 2" (50 mm) to 4" (100 mm) chips in a single step. It's cost-efficient, easy to use, and maintain.
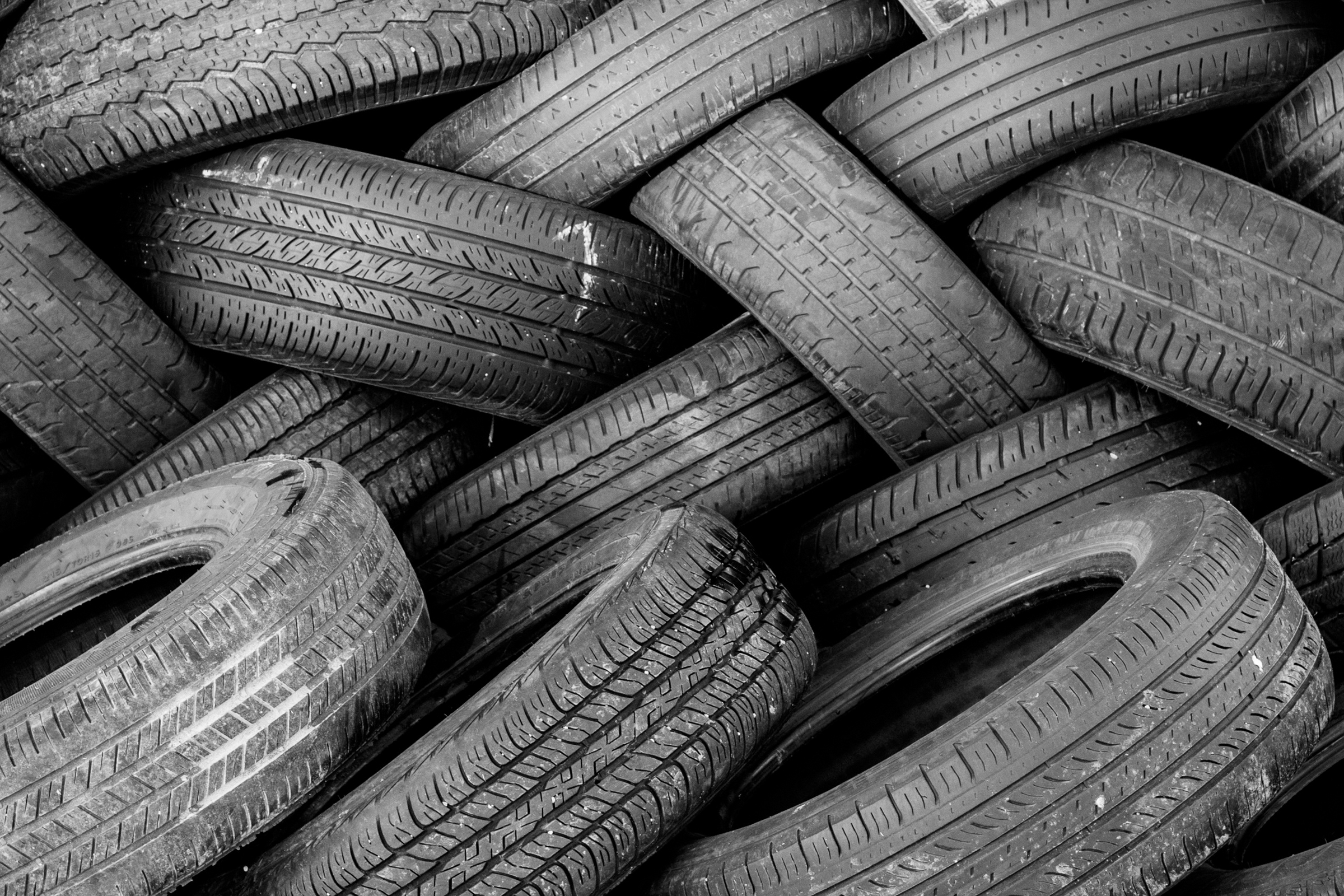
Find the right tire shredder
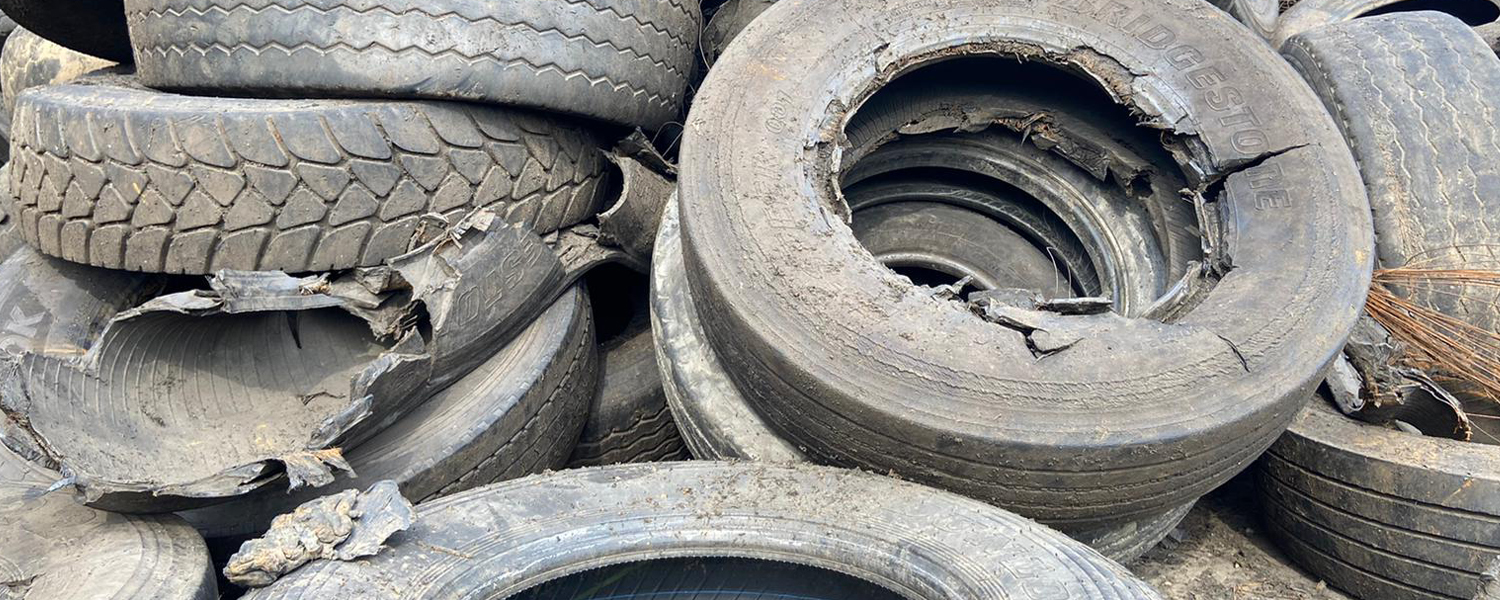
Rubber wastes and scrap tires in particular are a major problem worldwide. Every year around 1 billion used tires need to be disposed of and most of these are simply being dumped into landfills.
This not only hurts the environment but also wastes an extremely viable product. When properly shredded, tires and rubber provide not only a high BTU product for cement kilns, but have many other uses – cushioning playground material, wood replacement and building block additive (combined with recycled cement products), road base additive, high strength steel recycling, alternative daily cover, and many more!
A common problem within tire recycling encounter is that multiple units are required to process this seemingly difficult material because the different waste products in this category include scrap or even old tires, conveyor belts, rubberized chains and other production scrap. These normally contain a significant percentage of steel which needs to be liberated in the processing chamber and then separated by magnets after the shredded material passes through the sizing screen installed behind the rotor. This made a recycling facility a fairly expensive endeavor until the introduction of the UNTHA XR Series of single-shaft shredders.
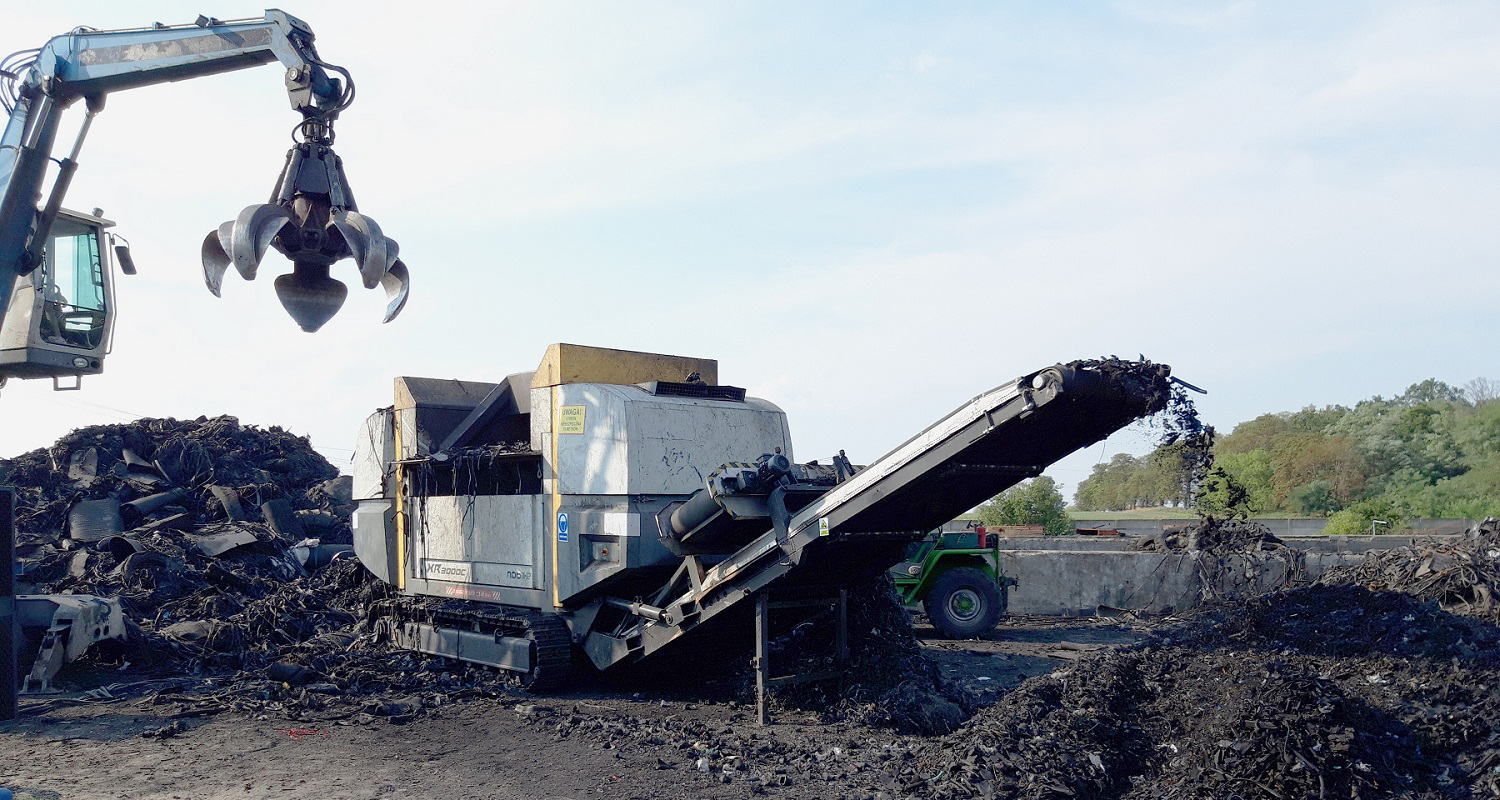
Tire Derived Fuel (TDF) for cement kilns
The demand for Tire Derived Fuel (TDF) is growing making them an ideal alternative fuel for industries with energy-intensive processes.
The incineration of scrap tires has some advantages: on the one hand, their high energy content makes them cheaper than coal; they produce a clean emission and have a low moisture content. Furthermore, tire ash residues contain less heavy metal than coal, and tire combustion leads to fewer NOx emissions compared to high sulfur coal combustion.
Cement manufacturers often have their fuel specifications.
A 50mm (2") clean-cut TDF chip with minimal crosshairs is a common burn-efficient fuel for a kiln.
Available as a static or mobile machine, a UNTHA tire shredder achieves variable product sizing – from a rough shred 100 mm chip through to a refined 50 mm TDF – within a single step.
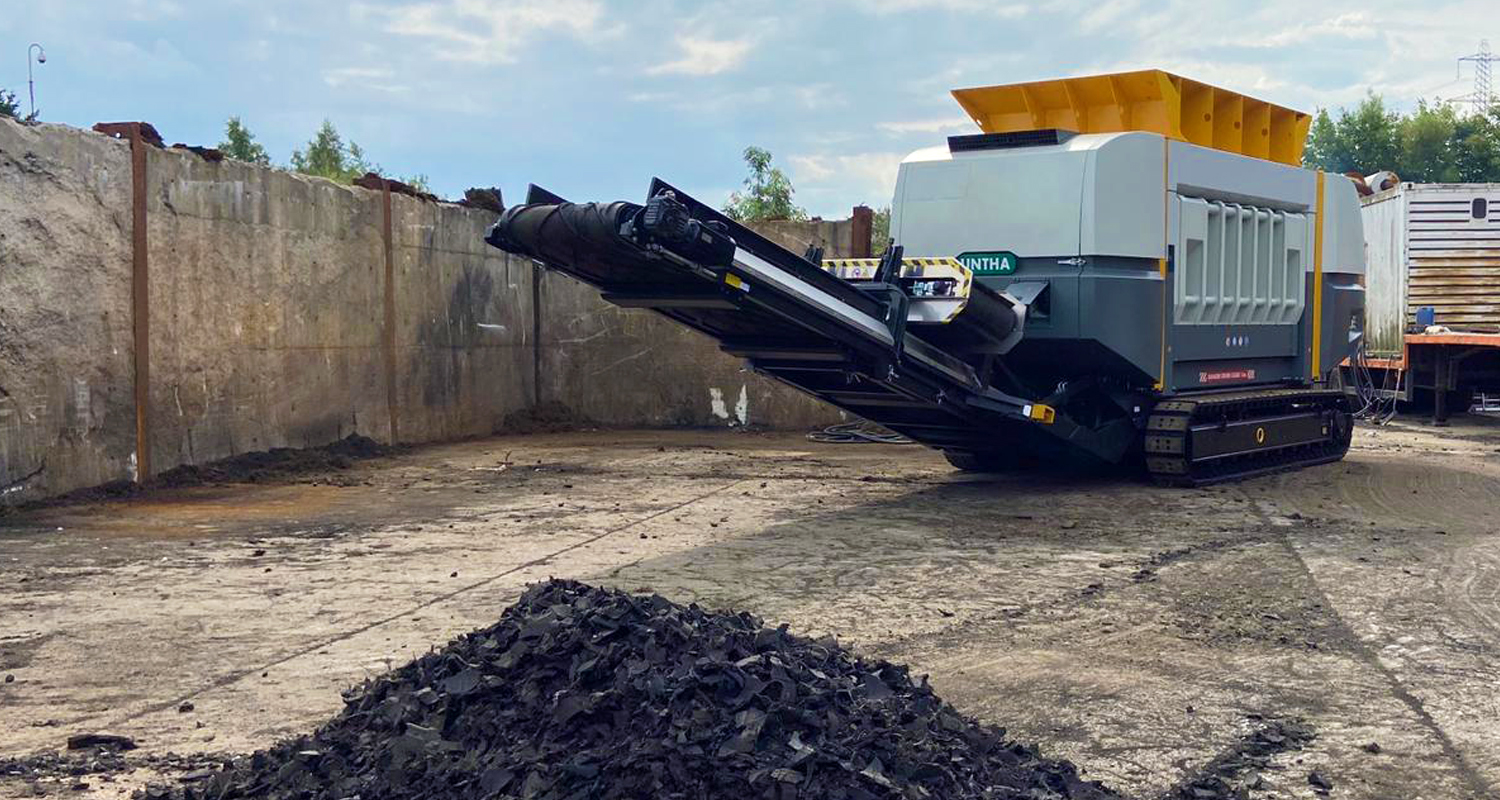
Complete tire recycling system
The XR3000C-HT with the High Torque Gear Box Configuration and “C” rotor with two rows of cutters provides a machine capable of effectively processing whole tires including the bead and other rubber wastes down to a 2” (50mm) minus end product in a single pass. The throughput rate is up to 10 TPH. An overband magnet can separate up to 80% of the wire in this configuration, which creates a high-value end product for use in cement plants and other markets.
This 2” minus material can then be processed by a UNTHA Model XR3000XC with a 4/5” (20mm) sizing screen to remove the remainder of the steel and create an extremely sought-after end product. It also enables the facility to further refine the tire wire to create another premium end product out of a waste stream that was otherwise considered “difficult at best” to shred.
In the end, tire shredding becomes profitable.