Material
Due to the different materials used and styles available, mattresses are difficult to shred/recycle effectively. This usually leads to them simply being thrown away rather than processed to reclaim the valuable materials trapped inside.
The XR can be configured to meet this challenge easily and profitably.
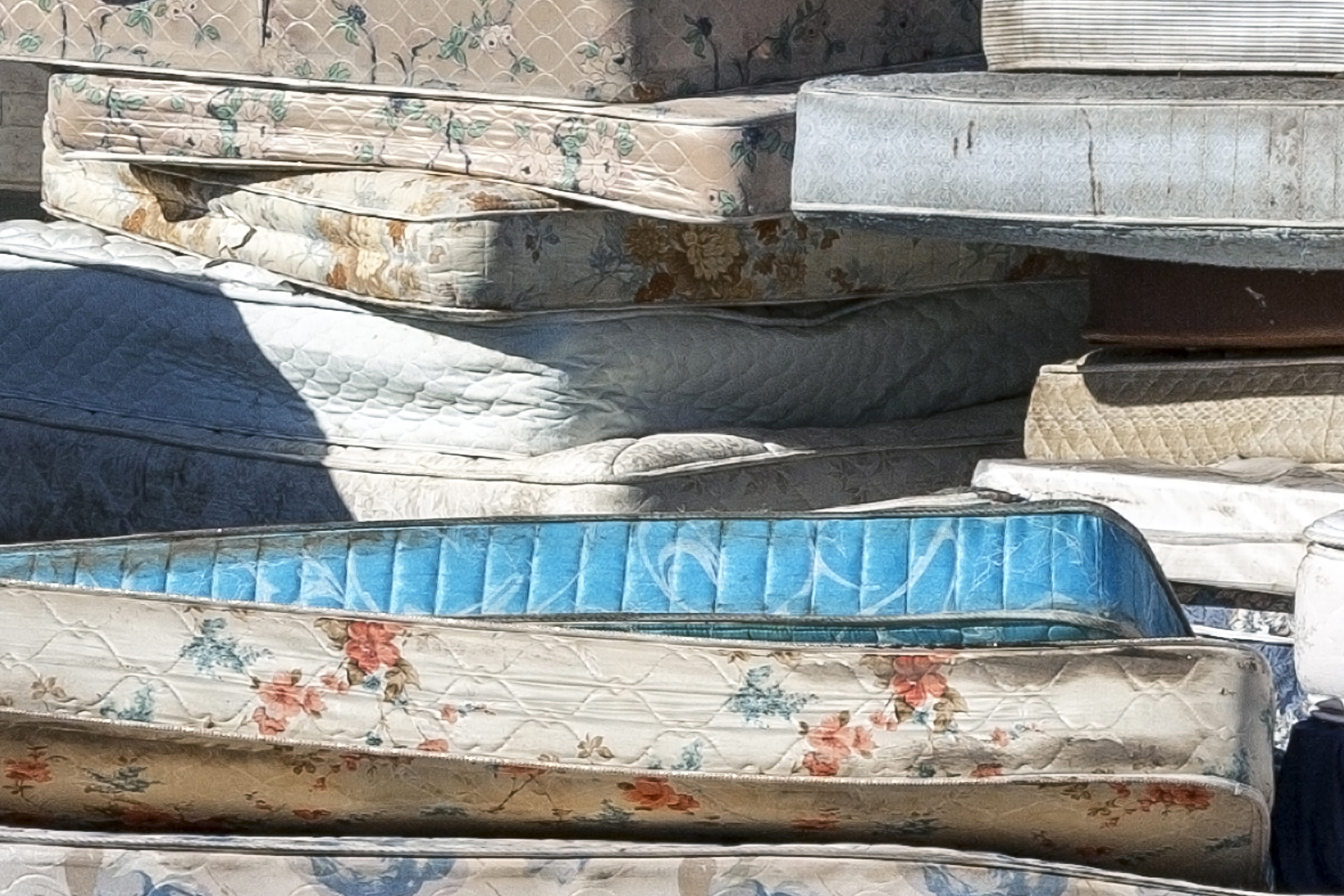
Find the right shredder
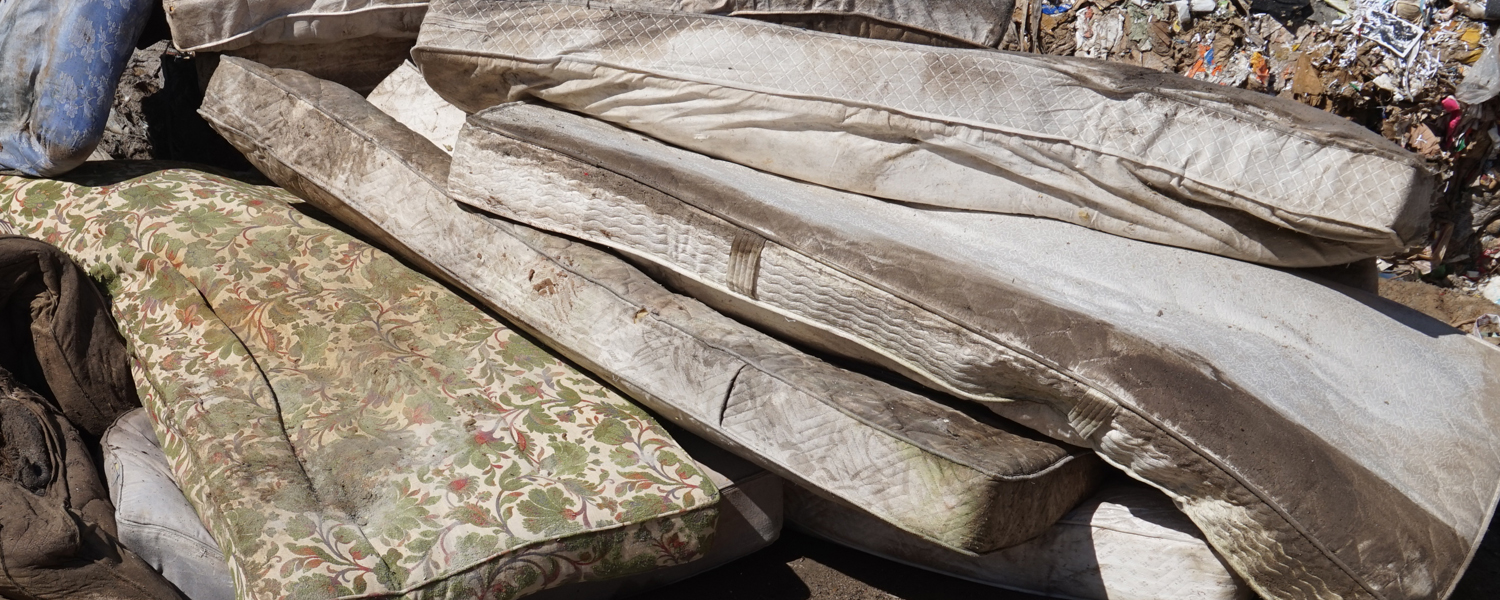
The range of materials in the mattress and the high tensile strength spring steel used in the coils makes shredding mattresses extremely challenging but if done properly, the liberation and separation of these components represents an extremely lucrative business.
In addition to the Mattress Recycling Council’s (MRC) involvement in driving this effort forward in the US, these components are highly sought after in several different markets- the foam components make an extremely valuable fuel; the flock is effective as a filtering agent or fuel and the spring steel commands a premium price from recyclers.
UNTHA is pleased to introduce the XR as a proven unit in this effort to prevent mattresses from simply ending up in landfills and their components not properly separated and value lost.
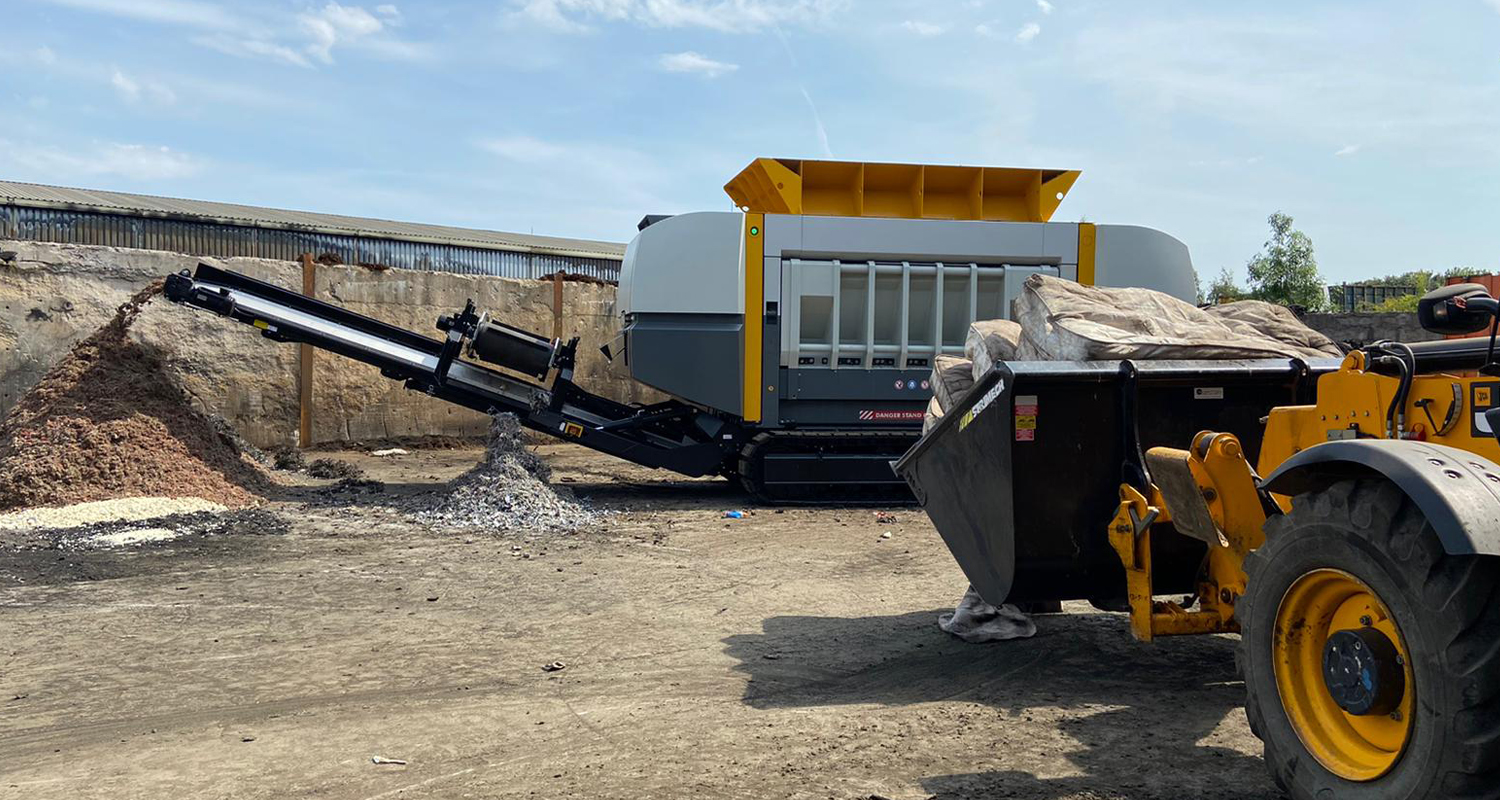
Equipped with a “C” rotor and high torque gearbox configuration, the Model XR3000 can effectively shred even pocket coil mattresses in a single step.
The 118” (3m) wide rotor equipped with the highest torque gearbox drives and two rows of cutters can process up to 200 mattresses per hour down to a 2” (50mm) end product size in one pass.
The slow rotor speed and superior torque available enable the unit to liberate the valuable products trapped in the mattress. The rotor and cutter design ensure that the materials do not wrap around the rotor so that a downstream magnet can separate the steel from the other components. A simple air separation system can further refine the end products to maximize their aftermarket value.
The remaining textile components make an excellent high BTU fuel for cement kilns and thermal power plants.