Customized shredding solution for Austrian manufacturer of furniture components
For expanding manufacturer SPEEDMASTER, based in Eberstalzell in Upper Austria, first-class technical solutions and an intelligent machine pool are fundamentals for providing customized solutions in record time. When it comes to shredding chipboard panels, the LR1400 wood shredder by globally active company UNTHA, headquartered in Kuchl/Salzburg, lives up to all these requirements.
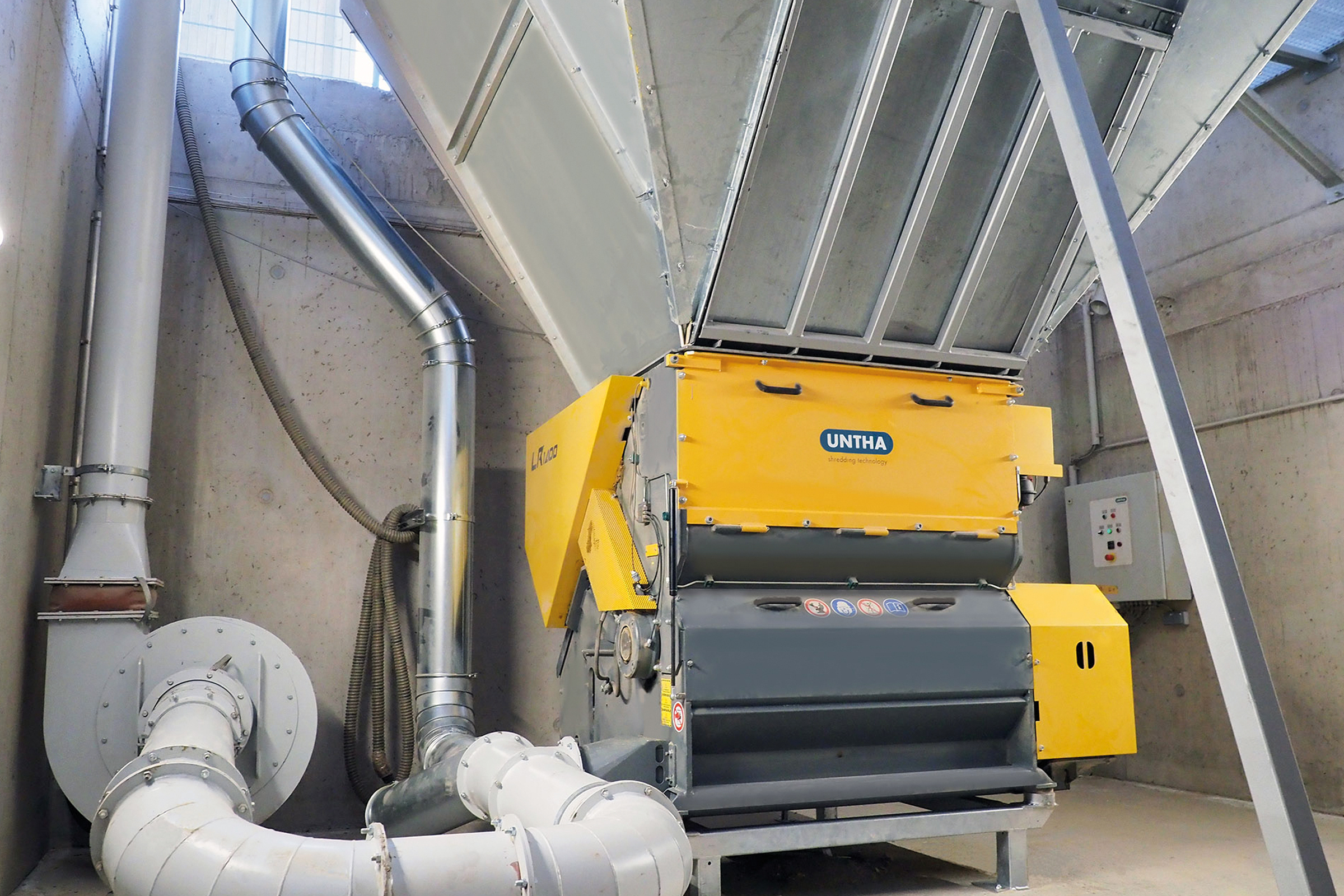
For SPEEDMASTER, speed and efficiency are key
SPEEDMASTER was founded in 1989 as a family enterprise specializing in classic joinery. Since then, the company has grown into one of the largest European producers of semi-manufactured parts. The company's state-of-the-art production sites in Germany and Austria are based around networked workflows and automation. Orders are placed online using a sophisticated IT solution. Within just 48 hours of the order being placed, the company produces a wide range of customized furniture components for further processing by joinery workshops. The company's emphasis on speed and outstanding quality standards relies on an optimized value chain and the use of first-class, innovative technologies. A sophisticated, highly efficient shredding solution is an important part of the smooth manufacturing process at SPEEDMASTER.
Efficient shredding of chipboard panels and residual wood
Outstanding efficiency and constant availability, both important factors in ensuring seamless workflows, were the most important requirements for SPEEDMASTER when the company decided to invest in a new shredder for their plant in Eberstalzell in 2017. All the machinery used by the company must be ultra-efficient in order to live up to the demanding standards in place at SPEEDMASTER, and the expectations for shredding chipboard panels and residual wood are equally high. With the UNTHA LR1400, an innovative and reliable solution was found.
UNTHA LR1400 scores extra points for reliability
Exchanging the cutters of the UNTHA LR1400 is quick and straightforward. The cutter holders are also easy to replace in case of damage caused by foreign matter and may be exchanged swiftly by the customer. The innovative cutter geometry and fasteners of the LR1400 are a big plus for optimized shredding and allow the efficient processing of wet wood, to name just one advantage. The positive fit of the cutters prevents the threads from becoming deformed. Two hydraulic cylinders of the LR1400 ensure that the pusher is pulled in simultaneously on both sides, eliminating the risk of the pusher becoming jammed. This sort of hydraulic ram construction eliminates the need for pusher guides and therefore also for wear parts. The tried-and-tested cutting chamber of the LR1400 guarantees a homogeneous granulate and attractive throughput values. Furthermore, UNTHA offers an extended warranty of three years for the LR1400 shredding solution.
Bespoke products that fulfil individual customer expectations
Every UNTHA solution is customized to fit individual requirements. This also applies to the solution that was chosen for SPEEDMASTER, where the loading process is somewhat unusual: The material is taken to a large hopper using an oversize forklift-mounted tipping trough. The machine is loaded on a fully automated basis and care must be taken to avoid bridging. The standard LR1400 comes with a mounted discharge screw conveyor that transports the material from the chopping unit to the interface with the suction system. This reduces the rated capacity required by the suction unit, making it more energy efficient. As an additional feature, a computer-controlled central lubrication system for the entire unit was installed, eliminating the need for manual lubrication after every 150 operating hours. The start and stop processes are also fully automated. Filling levels are measured by a light barrier: Once the defined minimum level is reached, the machine starts to operate. When the suction unit is empty, operation will cease. The LR1400 also comes with an integrated controller to avoid current peaks.
A perfect match: Clear decision in favor of UNTHA
SPEEDMASTER have been using the LR1400 for 18 months, to their utmost satisfaction. "The LR1400 has more than lived up to our requirements. For us, it was crucial that waste would be transported to the shredder in an automated process, and that significant fluctuations in volume and particle size wouldn't cause any issues", says Günther Schweiger, Managing Director at SPEEDMASTER. He is particularly impressed with the high throughput of the unit, which far exceeds expectations thanks to the combination of an ÜSS cutting system with a large, 35mm perforated screen. "The higher throughput is extremely advantageous for us and the unit performs much better than we expected. We really appreciate the excellent cooperation and the outstanding level of service provided by UNTHA!" Arno Urbanek, Product Manager at UNTHA, also sees the deployment of the LR1400 in the SPEEDMASTER plant in a highly positive light: "From the very start, we went out of our way to take all the requirements of this specific customer into account, and as a result we came up with a solution that perfectly reflects the SPEEDMASTER priorities."